Cost Comparison of Liquid vs. Gaseous Hydrogen: Expert Analysis of Heavy-Duty Fueling Applications
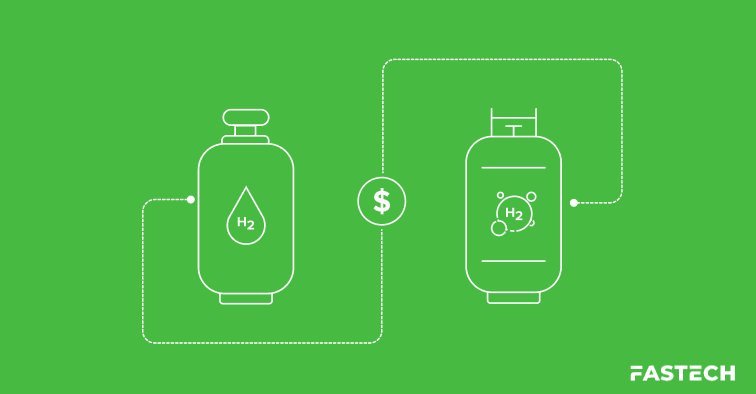
Developers of hydrogen (H2) fueling facilities face many strategic decisions, including location, facility size, and equipment selection.
One of the most pivotal decisions is whether to build a liquid hydrogen (LH2) or gaseous hydrogen (GH2) fuel station. Each entails unique cost variables—including storage demands, supply availability, development space, permitting requirements, and maintenance considerations.
This analysis focuses on LH2 and GH2 system development and maintenance costs among models with similar performance expectations in heavy-duty settings. We’ll also consider compliance with the guiding code established by the National Fire Protection Association (NFPA), for both gaseous and liquid systems.
Please note that supply availability and delivery costs are highly variable in this relatively new market and must be calculated case by case. Therefore, these variables are not discussed at length.
In summary, this analysis will provide quantitative and qualitative comparisons of equipment costs, operational efficiency, NFPA compliance, and overall reliability of GH2 and LH2 systems for heavy-duty applications.
Analysis Summary
Based on current market conditions and available technology (without considering hydrogen supply and logistics costs), LH2 systems are more cost-effective in heavy-duty fueling settings.
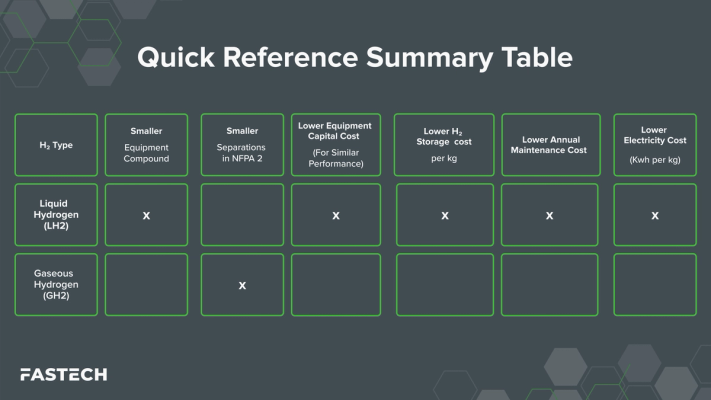
Analysis Notes
- GH2 systems can cost up to 40% more than LH2 systems for equivalent performance.
- The expected maintenance cost of GH2 systems is over two times higher on an annual basis than LH2 systems.
- Utility cost for LH2 can be as much as 40% less than GH2 systems with equivalent throughput.
- Even with boiloff, the cost of liquid H2 per kilogram after delivery is less but depends on the frequency of system use and cold H2 deliveries.
- Utilizing additional chilling equipment to manage and reduce boil-off is recommended and further enhances the LH2 option.
- The area required for LH2 equipment is less than GH2 alternatives, but the minimum facility space required is greater for LH2 due to NFPA requirements for larger setback (distance from property line).
- Larger setback requirements for LH2 systems are typically offset by the large space already needed for heavy-duty vehicle circulation.
Equipment Cost Comparison
Heavy-duty hydrogen fueling systems are in the early market stage of development. Currently, no commercially available hardware facilitates high-flow, heavy-duty protocols.
This limited availability is due to several contributing factors, but the primary factor is heavy-duty hydrogen vehicles being in a similarly nascent stage. Hence, investment in their fueling infrastructure is still in low demand. Additionally, high-flow fueling rate protocols that emulate diesel have only recently been developed.
Establishing typical pricing for heavy-duty fueling equipment is challenging, as market forces have yet to stabilize an average cost. The best available cost data is extrapolation from light-duty applications, which share many infrastructural similarities.
A common initial performance specification for a heavy-duty hydrogen fueling facility is outlined below:
- Demand throughput: 2,000 kg - 4,000 kg/day
- Storage: 4,000 kg LH2 or 2,000 kg GH2
- Fill rate: 4 kg - 8 kg/min per dispenser
- Parcel adequate for truck circulation
- Two fueling lanes
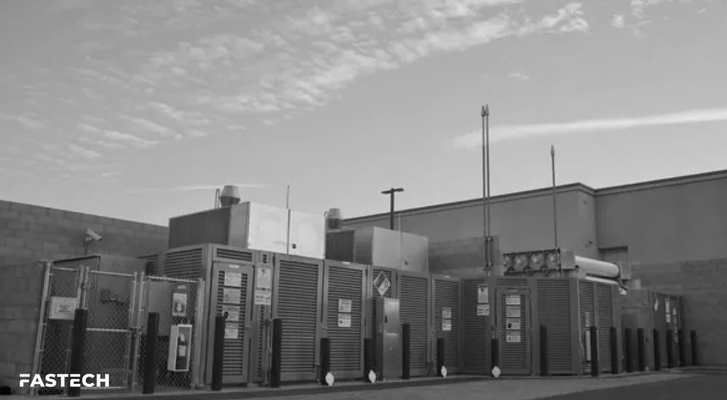
A typical LH2 equipment system package meeting the performance criteria listed above was recently quoted at $6 million—including pumps, piping, valve panels, electrical connections, dispensing, and two 240 kg/hr pumps to make a complete integrated package.
While this configuration is intended for use with two single-hose dispensers (4kg/min per hose), directing the flow to one dispenser theoretically achieves 8 kg/min, which meets heavy-duty marketplace expectations if the dispenser can accommodate this.
A best-in-class equivalent gaseous system with a popular packager was priced at approximately $10 million—including the compression, chilling, and dispensing units. This is an approximate 40% increase in cost from a similar LH2 system.
One of the primary reasons for this cost difference is the inefficiency of ambient temperature gaseous phase hydrogen compression compared to liquid phase cryogenic hydrogen pumping (less energy is required to compress a liquid than a gas).
With GH2 systems, all of the pre-cool required for J2601 protocol dispensing is generated from mechanical refrigeration systems. In LH2 systems, all pre-cool energy comes from the LH2 heat exchanger process.
Note that mechanical refrigeration systems are a source of maintenance and utility costs for gaseous applications. Again, supply and transportation must also be considered since hydrogen liquefaction requires a significant amount of energy—combined with transportation costs—which contribute significantly to per-kilogram pricing.
All hydrogen fueling facilities must maintain on-site storage for on-demand fuel supply. As of 2024, the approximate cost of hydrogen storage is as follows:
• Liquid H2 storage tanks - $200/kg
• Gaseous H2 storage vessels - $1,000/kg
Additionally, the equipment footprint for 4,000 kg of GH2 storage would be almost double that of equivalent LH2 storage.
Since gaseous hydrogen storage is more expensive, facilities typically mitigate the cost by installing smaller or fewer vessels and relying on frequent deliveries.
In short, liquid hydrogen systems cost less upfront, require less equipment, and offer superior operational efficiency in a heavy-duty environment.
Boil-off and Venting Comparison
According to the National Renewable Energy Laboratory (NREL), typical LH2 storage will boil off an average of 1% per day. The supply transfer process results in an estimated 15% loss of stored LH2, and heat produced from dispensing (pump compression, cavitation, and conveyance piping heat gain) results in an additional 2 to 3% product loss.
Gaseous H2 transportation, delivery, storage, and dispensing of results in little to no product losses. However, since GH2 transfers through differential pressure, the process is time-consuming (three or more hours) and inefficient. Only about 40-60% of the GH2 delivered to the site can actually transfer from the tube trailer, leaving the remainder to return to the supply point.
Further exacerbating this issue, the high-pressure storage vessels used for GH2 transportation are quite heavy, limiting the volume of fuel that can be delivered in a given trip (up to 500 bar in a 1,000 kg tube trailer without exceeding the 80,000 lb. gross vehicle weight limit).
Note that Hydrogen loses about one-third of its usable energy during the liquefaction process, compared to only one-tenth from gaseous compression (assuming the GH2 isn’t derived from bulk LH2).
However, commercial fueling facilities generally require large fuel transfer volumes, a demand that favors LH2 over GH2.
Engineering and Construction Cost Comparison
Generally speaking, the cost to engineer, permit, and construct a liquid or gaseous H2 fueling facility site does not differ much, if at all. The most significant cost variation comes from the chosen property’s specific features and constraints.
Overall, designing and permitting a hydrogen station is similar to any other commercial fueling facility. The primary governing code is NFPA 2 (discussed further in the next section), but other codes will apply depending on the government agencies involved.
One significant cost dependency is the degree to which the equipment package has been engineered for integration. When different OEM-supplied elements are combined without comprehensive regard for their integration and algorithms for operation and coordinated interaction—engineering and construction costs escalate. This is often due to troubleshooting and redesign work at the end of the project to achieve the intended system functionality.
Another cost consideration (no different from any development) is site location. Adding H2 systems in existing facilities can drive up costs due to NFPA 2 regulations and the need for more separation distance from (or protection of) existing assets.
When placing either LH2 or GH2 systems on greenfield properties or large open areas on existing developments, the essential costs to engineer and construct do not differ significantly.
NFPA 2 Code Applied
NFPA 2 is the guiding code document for hydrogen equipment. There are two ways to achieve compliance: the “Prescriptive” and “Performance Based” approaches.
The prescriptive approach utilizes the prescribed separation distances outlined in the respective chapters in NFPA 2 for liquid or gaseous H2.
The performance-based approach requires an equipment-specific study to determine defined specifications for the proposed equipment package and placement. These studies evaluate leak-related jet fire risks using gas dispersion models and often find that reduced separation distances can be used with adequate safety measures.
The prescriptive approach is considered the least expensive, as conducting the study can require a costly and exhaustive review of the chosen equipment. The performance approach is often considered if the same equipment is proposed for multiple locations, such as a multi-site program with many sites using the same design. The cost of the study can then be amortized over the number of sites.
The study might also be recommended when the equipment will be positioned in tight areas of existing facilities where every square foot must be optimized.
In general, NFPA 2 is more restrictive with LH2 than GH2. The restrictions in separation distances from sensitive receptors are defined for three different group types.
The table below (abbreviated and combined from tables in NFPA 2) illustrates the difference in regulations for typical liquid and gaseous heavy-duty bulk storage systems. Liquid H2 stored at >125 bar and gaseous H2 stored at > 7500 psi bar are standard criteria for heavy-duty applications.
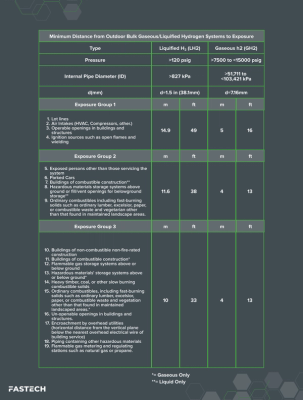
These distances correspond to the space or real estate needed to place H2 equipment. Due to the setback distances, a liquid hydrogen facility generally requires considerably more space.
NFPA 2 allows reductions for both liquid and gaseous hydrogen storage through the use of fire barriers (e.g., masonry walls); however, the modified separation distance difference is still substantially greater with LH2.
However, the direct costs of these requirements are often offset by heavy-duty facilities’ inherent need for large space. Since the parcel size needed for vehicle circulation is larger than the separation requirements, code compliance has less influence on equipment placement.
Utility Cost Comparison of LH2 vs. GH2
The energy used by either system depends on the fuel volume, the pressure levels of the supply site, and the tank of the delivery vehicle.
Cooling the gas in a GH2 system can account for as much as 40% of the energy cost. Whereby, the LH2 system can utilize the inherent cold temperatures of the LH2 to meet SAE J2601-5 requirements of filling vehicle tanks.
An energy comparison was derived with a basic analysis comparing GH2 and LH2 throughputs of approximately 8kg/min. The following graphs illustrate the contrast in energy costs between systems.*
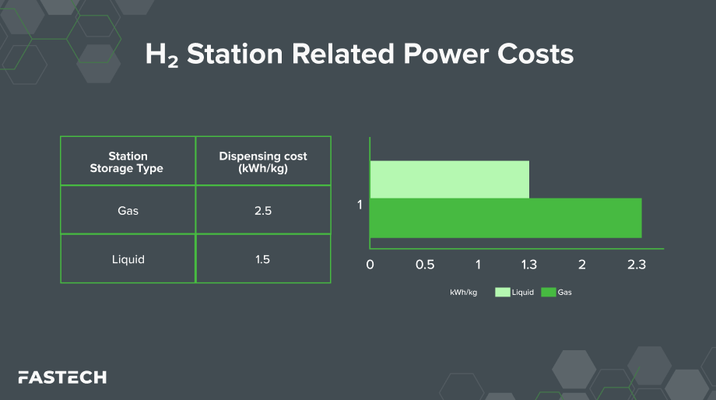
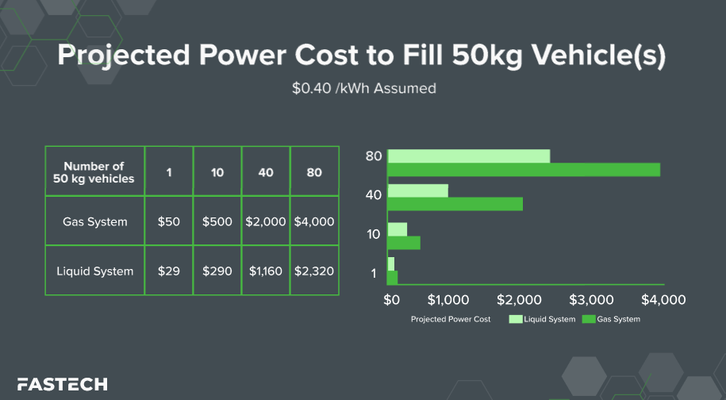
*These graphs only illustrate magnitudes of differences. Actual costs must be analyzed case-by-case using local utility costs, which can vary significantly.
Maintenance Cost Comparison of a 700 bar LH2 vs. GH2
Like any industrial equipment with moving parts—like pumps, compressors, and chillers—hydrogen station operation and maintenance costs are commonly proportional to the volume of use. Maintenance costs increase alongside the throughput of hydrogen and amount of commercial activity.
Gaseous systems typically have higher maintenance costs than their liquid counterparts. The major differentiator is the mode of fuel dispensing.
GH2 systems use compressors, while LH2 systems use cryogenic pumps with fewer valves and parts to service. Within GH2 systems, there is also significant variation based on whether they employ diaphragm or hydraulic piston compressors.
Diaphragm compressors are often chosen to ensure little to no cross-contamination between hydrogen and lubricating oils, thus maintaining fuel quality. However, they perform best under steady-state continuous operation. Under intermittent use, they are susceptible to more frequent failure. When the diaphragm fails, there is little to no warning. This can increase costs considerably since it is an unplanned maintenance activity that causes pump downtime.
Hydraulic piston compressors generally last longer under intermittent operations without major overhauls or repairs. These compressors also have a seal life whereby their integrity can be monitored, allowing for planned seal changes and prevention of surprise shutdown events.
Manufacturers publish mean time between failures (MTBF) for both pumps and compressors, serving as benchmarks for cost predictions. However, the times are imprecise due to limited data availability for heavy-duty hydrogen fueling systems.
Though anecdotal, FASTECH technicians have documented diaphragm compressors with an MTBF as low as 50 hours, whereas a 5-stage piston compressor reaches up to 500 hours.
LH2 cryogenic pumps typically run for over 1,000 hours without major repairs.
Pump rebuilds (evaluation and parts replacement or maintenance to return functionality) are another cost factor. With simpler system designs, an LH2 pump costs 30-50% less to rebuild than a GH2 compressor. The LH2 pump can be rebuilt in 1-2 days, whereas GH2 compressor rebuilds can take 2-3 days with the same labor crew.
GH2 systems generally need more compressors to achieve throughput equivalent to their LH2 counterparts, creating more potential failure points in a gaseous system.
GH2 systems require extensive refrigeration/heat exchange systems for compressor cooling and pre-cooling to meet J2601 dispensing requirements. Most systems use either R410, R507, or CO2 as refrigerants—and EPA regulations require strict protocols for managing the refrigerant gas replacement process.
Conversely, LH2 systems utilize cold temperatures from the liquid and a heat exchanger to achieve the proper temperature for J2601 gas dispensing without a mechanical chiller unit, eliminating a substantial portion of the maintenance cost.
The following table compares the typical maintenance cost of two similar facilities in terms of H2 throughput. The costs are a general comparison. Results will vary from site to site depending on the location, H2 throughput, and the degree of preventative maintenance performed.
FASTECH always encourages preventative maintenance to minimize unexpected failures, which often exacerbate the repair costs.

As a general rule, the maintenance cost of a GH2 system can be as much as 2.5 times the cost of an equivalent LH2 system on an annual basis.
LH2 vs. GH2 Performance Summary
Liquid hydrogen (LH2) fueling systems offer a significant cost advantage. On average, they are 40% less expensive than gaseous hydrogen (GH2) systems while maintaining equivalent performance. Liquid systems are also generally more reliable and affordably maintained because they have fewer components and, thus, fewer points of failure.
Additionally, LH2 storage is more cost-effective per kilogram and requires less space compared to gaseous storage. Currently, most market equipment is designed according to SAE standards that allow for filling rates of 60g/sec (3.6 kg/min), although a new protocol permits rates up to 300g/sec (18 kg/min), which has yet to be demonstrated in practice.
Some LH2 systems are capable of achieving filling rates between 8-10 kg/min, with several commercial projects in the planning stages. LH2 systems typically maintain continuous filling without interruption; for instance, a cryogenic pump rated at 240 kg/hr (4 kg/min) could fill an average of four trucks per hour under optimal conditions.
In contrast, GH2 systems depend heavily on high-pressure gas storage for initial filling. Once this storage is depleted, the filling process may slow down or require a wait for compression, which can be particularly challenging at busy fueling stations requiring significant high-pressure storage capacity.
FASTECH’s Role in Hydrogen Fueling Station Development
FASTECH partners with industry trailblazers like Shell, Chevron, and Toyota to deliver future-ready alternative energy solutions. With over 40 hydrogen fueling stations built to date, the team’s renewable energy infrastructure expertise is among the nation’s forefront.
Though still in its early stages, hydrogen fuel is already revolutionizing what the heavy-duty transportation industry can achieve. Long-haul trucking, cargo management, and utility providers worldwide are already adopting clean hydrogen solutions.
For end-to-end hydrogen infrastructure EPC+M solutions—unlock the future of fueling with FASTECH.